Anaerobic DACS® and MBBR solution for Hall and Woodhouse Brewery
„Aqana´s patented Downflow Anaerobic Carrier System (DACS) with its unique simple but very efficient and robust technology set a new standard in the anaerobic wastewater treatment plant sector. helping us tremendously with the cost of biomass, chemicals, and energy. It was the best and only available solution that could meet our requirements regarding limited space (designated building), discharge limits, and stable operation even in a brewery, where we are faced with significant deviations of effluent conditions like COD, pH, solids, temperature, etc. The system has a very high COD removal efficiency of up to 95 %, a high methane purity of about 90%, and performs perfectly. Aqana helped us to meet important environmental regulations of the municipality and the government“- Toby Heasman, Head Brewer, Hall & Woodhouse Brewery, Dorset, UK
Today’s best practices in wastewater treatment solutions embody a number of key objectives, such as operational efficiencies, environmental impact minimization, and where possible, the potential for waste-to-energy generation.
The Challenge
This project was to replace an existing CSTR anaerobic reactor – that had been operating at Hall and Woodhouse brewery for over 15 years – with a new anaerobic wastewater treatment system.
A limiting factor was that the new anaerobic system had to be constructed on a small parcel of land on the brewery site, not breach local planning restrictions and continue to discharge to the existing sewer via a new sewer connection that was to be linked to the proposed new housing development.
The parcel of land was adjacent to a large supermarket and a law firm office; housing was also nearby, so the decision was made to shroud the plant in a corrugated steel building – essentially to hide it.
- The proposed plant should fit into the odd-shaped land available to build on (triangle)
- The proposed plant should not cause planning issues with height (e.g. higher EGSB reactors)
- The CAPEX and OPEX should be the most competitive
- Influent is sometimes loaded with solids like kieselguhr etc.
As a historic and renowned independent brewery in the UK – Hall & Woodhouse – was looking to replace its wastewater treatment plant as part of the brewery’s expansion and modernization program. The brewery assessed a wide range of possible treatment technologies, before deciding on an anaerobic process that provided the best available technology solution, which could also meet their operational needs and limited land on which to build a new wastewater treatment plant.
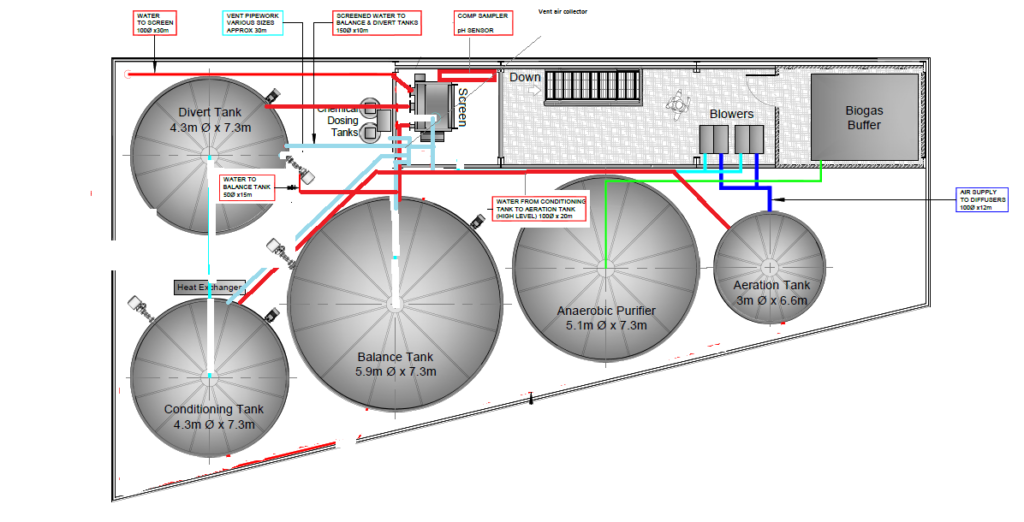
Figure 1. Wastewater treatment building layout
The Aqana Downflow Anaerobic Carrier System (DACS) was selected, because it offered the brewery number of important operational and performance benefits, including a small footprint and an attractive source of revenues for the brewery, in the form of renewable energy and associated ‘green’ tariff’s.
The new treatment plant also includes an Aqwise MBBR ‘polishing stage’ prior to discharge to the sewer. This simple low-cost design change improved the operational reliability of the DACS plant almost immediately following recommissioning of the wastewater treatment plant.
The WWTP plant was designed to be fully automated, including remote access via telemetry. The biogas created by the DACS plant is combusted in an integral CHP plant. The brewery takes the green tariff benefits from the heat and electricity that the CHP plant generates in the form of FiT’s and RHI’s. The DACS plant reliably meets contractual obligations for both treated water quality and biogas generation.
The Process
DACS is a unique anaerobic treatment process, using high-performance flocculated anaerobic biomass, captured within a proprietary carrier system.
Wastewater, with entrained biological solids, flows into the DACS reactor through a simple pipe distribution system, located at the top of the reactor. From here, the wastewater passes by gravity down through the fluidized carrier bed – the treated wastewater passes out from the DACS reactor near its base, with most of the COD removed by anaerobic conversion to biogas.
Design criteria:
- Flow [m3/d] – Up 445
- Load [kg COD/d] – Up 2175
- Biogas [m3/d] – Up to 760
- Methane [%] – Up to 85
The down-flow action also helps to prevent the liberation of CO2 and H2S within the process reactor, consequently improving biogas quality.
All the biogas created by the DACS anaerobic treatment plant is combusted in a Combined Heat and Power system – the products of combustion are electricity and heat energy, both of which are reused by the brewery.
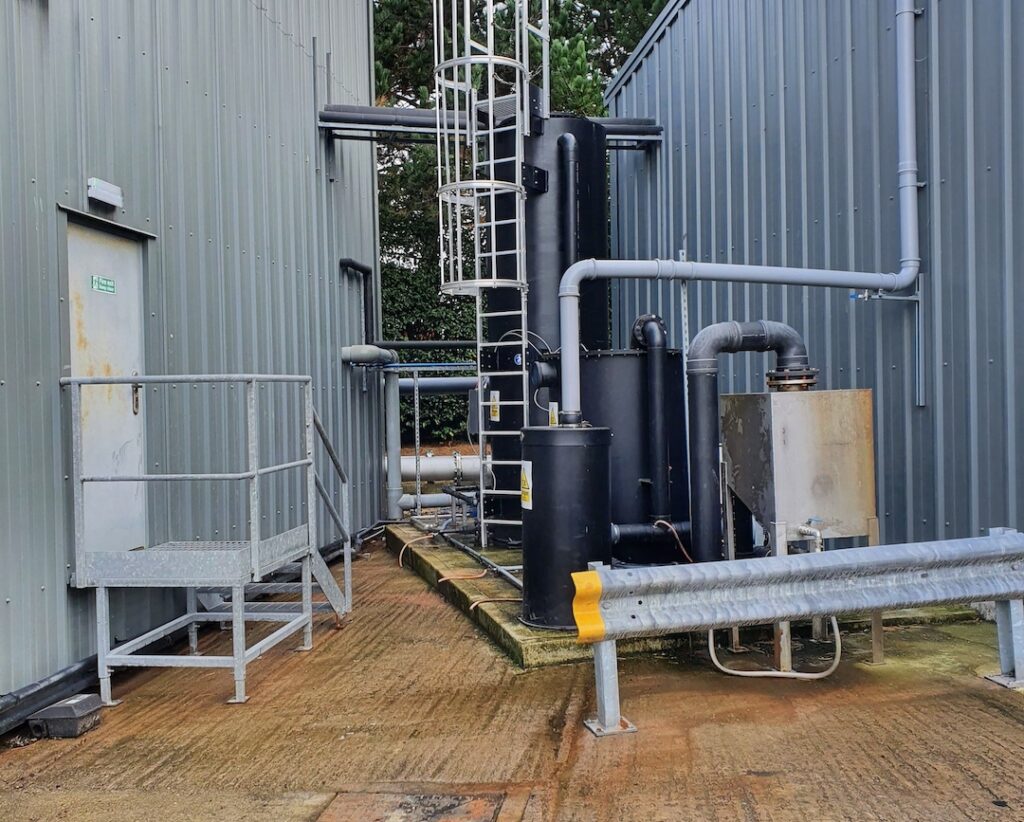
Picture 1. Treatment plant building and odor control unit
The DACS treatment plant was designed to fit within a relatively small section of land that was available to the brewery and meets the local planning requirements, including limits on height and general visual impact. The complete operational plant is enclosed within a bespoke and self-contained building, providing the lowest possible environmental impact.
The treatment building air is evacuated on a continuous basis and directed through an odor control plant before safe discharge to the local environment.
The anaerobically treated wastewater passes through an Aqwise AGAR-MBBR aeration stage before being discharged into the sewer. The DACS solution was designed to meet the brewery’s changing operational needs and has evolved to operate from an initial 5 days to the current 7 days per week.
The brewery operations team has stated that the DACS system is a vast improvement on their original CSTR anaerobic system, stating that it operates in a safe, clean environment and requires minimal operator attendance.